Nachhaltige Produktion bei Kling Malz
Neben vielen anderen zählt die Malzindustrie zu den energieintensiven Branchen. Das liegt vor allem an dem für die Malzherstellung notwendigen Trocknungsprozess, bei dem große Mengen Wasser zu verdampfen sind.
Die Verdampfungsenthalpie des Wassers bei 25 °C beträgt 2.546,5 kJ/kg (0,707 kWh/kg Wasser). Geht man davon aus, dass für eine Tonne Fertigmalz 750 kg Wasser (45 % GM Feuchte (wet basis)) zu verdampfen sind, so ergibt sich pro Tonne Fertigmalz ein Wärmeenergiebedarf von 530 kWh (bzw. 45.580 kcal/dt).
Weil der Trocknungsprozess in den letzten Phasen der Trocknung (Hygroskopie) nicht ideal verläuft, wird dieser Energieverbrauch noch überschritten. Die Trocknung mit Luft ergibt für die oben genannte Verdunstungstemperatur nach Wärmerückgewinnung schon einen Wärmeverbrauch von 603 kWh pro Tonne Fertigmalz.
Technische Einzelheiten finden Sie hier im Mollier h,x - Diagramm.
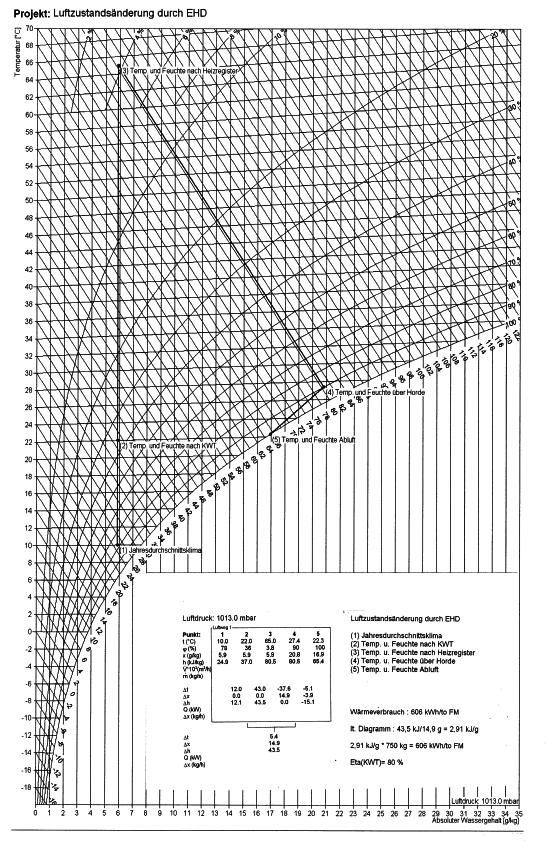
Vor dem Hintergrund dieser immensen Energieverbräuche sind Maßnahmen zur Verminderung des Strom – und Wärmebedarfs von großer Bedeutung.
Entscheidende Investitionen, die von uns in der jüngeren Vergangenheit getätigt wurden, um günstigere Verbrauchswerte zu erreichen:
Der Bau einer innovativen Doppeldarre 1988. Zwei luft- und wärmetechnisch gekoppelte Einhordendarren führen zu sehr günstigen Wärme- und Stromverbrauchswerten. Diese erste Luftumkehrdarre überhaupt ist immer noch bestmöglicher Stand der Mälzerei-Technik.
2007 die Inbetriebnahme eines Pflanzenöl Blockheizkraftwerks, welches im Rahmen eines Contracting-Verfahrens eine weitere Wärmequelle für die Mälzerei darstellt.
2010 die Investition in einen neu konstruierten Kreuzstromwärmetauscher ( HiF- KWT ), der gegenüber der alten Bauweise bei gleichem Druckverlust einen höheren Temperaturwirkungsgrad hat
Der Bau eines Weichwassererwärmers, der ein weiteres Absenken der Rauchgaswärmeverluste ermöglichte. Diese Idee wurde bei Kling-Malz entwickelt und verbreitete sich schnell in der gesamten Branche.
2011: Neubau einer Kälteanlage in Edingen. Umstellung auf das umveltverträglichere Kältemittel R134a
2016 die Investition in einen neuen Brenner, der gegenüber dem alten eine größere Regelungsbreite hat, und somit eine Verlängerung des energiesparenden Verbundbetriebs ermöglichte.
Neben diesen technischen Investitionen wurde ein effektives Energiemanagement-System eingeführt. Beide Produktionsstandorte betreiben erfolgreich ein
Alternatives System nach SpaEfV.